При выборе клеев для металлов необходимо учитывать следующие условия:
1. Клеи не должны вызывать (или способствовать) коррозии металлов.
2. Металлы не должны оказывать каталитического влияния на процессы отверждения клея.
3. При отверждении клея нежелательно выделение летучих веществ.
4. Для лучшего заполнения микронеровностей поверхности вязкость клея должна быть невысокой, но достаточной для образования прослойки требуемой толщины.
5. Для лучшего восприятия соединением деформаций (температурных и др.) прослойка отвержденного клея должна быть достаточно эластичной.
6. Состав клея должен обеспечивать получение прослоек, обладающих максимальными показателями прочности.
Форма и поверхность металлических деталей, подготавливаемых к склеиванию, также
должны удовлетворять определенным требованиям. На поверхности их не должно быть ржавчины,
окалины, следов от фрезерования или штампования, выбоин от молотка и других вмятин. Чтобы
получить ровный и относительно тонкий клеевой шов, детали должны плотно прилегать одна к
другой, т.е. смежные поверхности их должны быть ровными и гладкими. На деталях нельзя
оставлять односторонние заусенцы, так как они препятствуют плотному соединению поверхностей.
Особые трудности возникают при склеивании больших листов. Кромку листов, как правило,
рихтуют, выравнивают, после чего в металле остаются внутренние напряжения, дополняющие
напряжения от рабочих нагрузок. Вследствие этого клеевое соединение может разрушиться даже
при сравнительно небольших рабочих нагрузках.
Если при склеивании детали входят одна в другую, например в цилиндрических и пазовых
соединениях, между ними должен быть зазор от 0,1 до 0,3 мм. При более точной подгонке
деталей зазоры могут быть меньше 0,1 мм. При вклеивании деталей в углубления воздух должен
быть удален (не через зазор!), иначе клеевой шов будет неплотным.
Исключительно важно подготовить поверхности металлов к склеиванию. В процессе
изготовления, транспортирования, хранения, обработки металлов на поверхности их образуются
оксидные пленки, осаждаются пыль, жир, адсорбируются влага, газы и другие вещества,
препятствующие смачиванию металла клеем. Так как получить совершенно чистую поверхность
металла практически невозможно, основной целью подготовки деталей к склеиванию является
активизация поверхности, заключающаяся в удалении пленок и наслоений, в замене среды, в
которой может происходить адсорбция.
В процессе очистки под влиянием среды (водной, воздушной, органических растворителей
и их паров, инертных газов и в вакууме) поверхность металла приобретает в ряде случаев
новые свойства, например способность адсорбировать гидрофильные вещества вместо гидрофобных
(водоотталкивающих). Толщина вновь образованных (адсорбированных) слоев должна быть
минимальной, так как от нее зависит прочность сцепления клея с поверхностью.
Адсорбированные слои, как правило, химически не соединяются с клеем, поэтому клеевые
соединения разрушаются по этим слоям. Утолщение адсорбированных слоев происходит наиболее
интенсивно в начальных стадиях адсорбции, поэтому клей следует наносить сразу после
окончания обработки поверхности.
Оксидные пленки, сцепление которых с металлом весьма различно, также влияют на
прочность склеивания. Обычно такие пленки (ржавчина, окалина) отстают от металла вместе с
клеевой прослойкой. Прочность соединения при этом невысокая. В других случаях после
тщательного обезжиривания достигается нужная прочность, даже при наличии оксидной пленки на
металле, однако при этом наблюдается сильный разброс результатов механических испытаний.
При подготовке поверхности металла к склеиванию применяют два вида обработки:
механический и химический. Выбор способа обработки того и другого вида зависит от степени
ответственности соединения, величины и характера его нагружения в эксплуатации. Обычно
каждое изделие обрабатывают и механически, и химически.
Механическая обработка состоит из очистки поверхности металла абразивными
инструментами (наждачными кругами, брусками, бумагой), напильниками, песком, пастами,
металлическими опилками, щетками и т.п. Способ обработки выбирают, учитывая коррозионную
стойкость и твердость металла. Грубая механическая обработка, в том числе пескоструйная,
оставляет глубокие риски (углубления) на поверхности некоторых мягких металлов, что
способствует в дальнейшем прониканию агрессивных сред под клеевой слой. При тонкой
очистке (шлифовке) поверхность становится намного ровнее, глубина микровпадин лежит в б
олее узких границах, а это повышает стойкость, герметичность и длительность сопротивления
клеевых соединений.
Предложен вибрационный способ механической обработки, заключающийся в том, что
наполнитель в клее, обладающий абразивными свойствами, при вибрации соединения очищает
поверхности, на которые нанесен клей. Продукты очистки и наполнитель остаются в отвержденной
клеевой прослойке.
Химическая обработка поверхности заключается в растворении жировых и других
наслоений, травлении оксидных пленок, нанесении гальванических покрытий.
Средства обезжиривания должны быть легко летучи, по возможности безвредны, обладать
высокой растворяющей способностью, не реагировать с металлом. Для обезжиривания применяют
ацетон, бензин, керосин, петролейный эфир, трихлорэтилен, перхлорэтилен, водно-щелочные
растворы (мыла и т. п.), а также эмульсии воды в бензине, уайт-спирите, керосине. В
некоторых случаях обезжиривание эмульсиями более эффективно, чем органическими
растворителями, так как жировые вещества не только растворяются, но и эмульгируются.
Необходимо учитывать и то, что эмульсии дешевле органических растворителей.
Ацетон, бензин и другие общеизвестные растворители используют при ручной обработке
поверхности деталей. Недостатком этих средств очистки является воспламеняемость,
взрывоопасность паров. Трихлорэтилен обладает чрезвычайно малым поверхностным натяжением,
поэтому легко проникает, особенно в парообразном состоянии, в мельчайшие поры. Он
невзрывоопасен, но пары его токсичны. Длительность обработки парами трихлорэтилена 5 мин.
Водно-щелочные растворы менее опасны, однако и они могут вызвать коррозию металла. Поэтому
после обработки этими растворами детали рекомендуется прополаскивать в теплой воде.
Водно-щелочные растворы состоят из тринатрийфосфата (50-70 г/л), жидкого стекла (25-30 г/л)
и жидкого мыла (3-5 г/л). Обработка производится в течение 3-5 мин при 75-80 °С.
В тех случаях, когда допустим длительный контакт металлов с водой, для очистки поверхности
применяют также моющие средства ОП-4, ОП-7 или ОП-10. Очищают изделия моющими средствами при
помощи волосяных щеток и других приспособлений. Детали сложного профиля, у которых в
мельчайших углублениях могут сохраниться остатки моющих средств, вызывающих коррозию,
тщательно промывают после обработки.
Механическое воздействие и обезжиривание сочетает ультразвуковой метод очистки.
Детали загружают в бак с водным раствором моющих средств или с органическим растворителем.
Очистка осуществляется при непрерывном протекании обезжиривающего средства через бак, в
котором возбуждаются ультразвуковые колебания удельной мощностью 5-10 вт/см².
Колебания передаются с жидкости на деталь, и частички наслоений отделяются от поверхности и
удаляются раствором. Необходимо иметь в виду, что в зависимости от размеров очищаемых
деталей или вида загрязнения частота колебаний должна быть разной. В процессе циркуляции
обезжиривающее средство фильтруется. Такая технология обеспечивает высокую
производительность и хорошую очистку. Так как установки довольно дороги, их использование
оправдывается только при серийной обработке сложных деталей.
Для удаления окалины, оксидных пленок и продуктов коррозии с поверхности стали,
меди, никеля, алюминия, вольфрама и сплавов используют травление в растворах серной,
соляной или азотной кислот. Перед травлением поверхность металла тщательно обезжиривают.
Ниже указывается последовательность операций, а также составы растворов при очистке
поверхности различных металлов.
Углеродистая сталь: 1 - обезжиривание в щелочном
растворе; 2 - тщательное прополаскивание в воде при комнатной температуре; 3 - погружение
на 2-4 мин при 15-22 °С в раствор, состоящий из 10 об. ч.
серной кислоты (пл. 1.84), 10 об.ч. азотной кислоты (пл. 1.42) и 80 об. ч.
дистиллированной воды; 4 - тщательное прополаскивание в воде (18-20 °С);
5 - погружение на 30-60 сек в раствор, состоящий из 50-60 об. ч. соляной кислоты плотностью
1,26; 2 об. ч. 30%-ной перекиси водорода, 38-48 об ч. дистиллированной воды; 6 -
тщательное прополаскивание в холодной, а затем в теплой (55 °С)
воде и высушивание.
Нержавеющая сталь: 1 - обезжиривание в щелочном
растворе; 2 - тщательное прополаскивание в холодной воде; 3 - погружение на 10 мин в
раствор (60-65 °С), состоящий из 46 об. ч. концентрированной
соляной кислоты, 10 об. ч. формалина, 2 об. ч. перекиси водорода, 42 об. ч.
дистиллированной воды; 4 - тщательное прополаскивание в холодной воде и высушивание.
Алюминий и его сплавы: 1 - обработка в парах
трихлорэтилена в течение 5 мин; 2 - промывание в воде при 60 °С
в течение 20 мин; 3 - двойное прополаскивание в холодной воде в течение. 5 мин; 4 -
травление в течение 20 мин в растворе (60 °С),
состоящем из 27,3 вес. ч. серной кислоты (пл. 1,84), 7,5 вес. ч. бихромата нагрия,
65,2 вес. ч. дистиллированной воды; 5 - двойное прополаскивание в холодной воде в течение
5 мин; 6 - кратковременное прополаскивание в горячей воде (60 °С);
7 - в ысушивание в потоке теплого (60 °С) воздуха в течение
30 мин.
Ускоренный метод обработки поверхности алюминия: 1 - обезжиривание органическим
растворителем; 2 - погружение на 1 мин в раствор (20 °С),
состоящий нз 4 вес. ч. фтористого натрня, 25 вес. ч, азотной кислоты, 71 вес. ч.
дистиллированной воды; 3 - прополаскивание в холодной воде; 4 - погружение на 1 мин в
раствор (60 °С), состоящий из 30 вес. ч. серной кислоты, 8
вес. ч. бихромата натрия, 6 вес. ч дистиллированной воды; 5 - тщательное прополаскивание в
холодной воде и высушивание.
Магний: 1 - обезжиривание в трихлорэтилене; 2 - погружение
на 10 мин в раствор (80 °С), состоящий из 6 вес. ч.
метасиликата натрия, 3 вес. ч. гидроокиси натрия, 3 вес. ч. тетрапирофосфата натрия, 1 вес.
ч. поверхностно-активной добавки, 300 вес. ч дистиллированной воды; 3 - промывание в
проточной воде, 4 - погружение на 15 мин в 20%-ный горячий раствор трехокиси хрома
(65 °С); 5 - трехкратное прополаскивание в дистиллированной
холодной воде; 6 - погружение на 30 сек в кипящую дистиллированную воду; 7 - высушивание на
воздухе.
Латунь: 1 - обезжиривание трихлорэтиленом; 2 - погружение
на 2-4 мин в раствор (20 °С), состоящий из 15 об. ч.
42%-ного раствора хлорного железа, 30 об. ч. концентрированной азотной кислоты, 97 об. ч.
дистиллированной воды; 3 - тщательное прополаскивание в холодной и теплой воде и
высушивание.
При склеивании бронзы и цинка лучшие результаты дает механическая обработка:
шлифование и очистка металлическими щетками. Оставшиеся на поверхности частицы удаляются
прополаскиванием в щелочном растворе или бензине.
Вода во всех случаях должна быть мягкой или умягченной.
Один из эффективных методов подготовки поверхности металлов к склеиванию - нанесение
гальванических покрытий, в частности анодирование поверхности. Повышенная адгезия многих
клеев к анодным пленкам объясняется их большей по сравнению с необработанными металлами
полярностью.
От способа обработки поверхности зависит прочность склеивания металлов. При
механической обработке твердых металлов (сталь, чугун) наилучшие показатели получают при
обдувании песком или металлическими опилками и грубом шлифовании наждачным кругом или
наждачной бумагой. При тонком шлифовании и полировке прочность соединения этих металлов
может снизиться в 2-3 раза по сравнению с грубым шлифованием. Для некоторых чувствительных
к механической обработке металлов (свинец, медь) и сплавов (латунь) грубая обработка
неприменима ввиду образования чрезмерно неровной ослабленной поверхности. Грубая обработка
дает хорошие результаты большей частью при склеивании клеями холодного отверждения. Клеи
горячего отверждения требуют чисто обработанной поверхности с неровностями порядка 10 мк.
От степени шероховатости поверхности зависит толщина клеевой прослойки, влияющая в
свою очередь на прочность клеевых соединений металлов. Наибольшая прочность получается при
достаточно малой толщине клеевой прослойки. Так, при уменьшении средней толщины клеевой
прослойки от 600 до 40 мк предел прочности соединения стали со сталью на феноло-каучуковом
клее горячего отверждения возрастает в 2,5 раза (рис. 1).
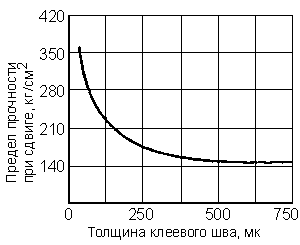
Рис. 1. Зависимость прочности соединения стали со сталью от толщины клеевой прослойки на феноло-акрилонитральном клее горячего отверждения
Величина крутящего момента, передаваемого цилиндрическим сопряжением стальных
шлифованных деталей, скрепленных эпоксидным клеем горячего отверждения, при одних и тех же
показателях чистоты обработки поверхности также возрастает при уменьшении толщины клеевой
прослойки (рис. 2). Поскольку напряжения сдвига при кручении мало искажаются под влиянием
геометрических характеристик соединения, то прочность его изменяется закономерно по
параболе в интервале толщин клеевого шва от 10 до 180 мк.
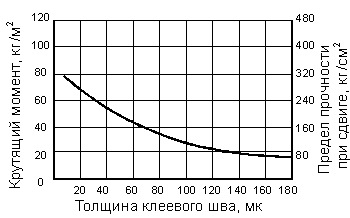
Рис. 2. Зависимость величины передаваемого крутящего момента от толщины клеевой прослойки в соединении на эпоксидном клее стального стержня диаметром 19 мм со стальной втулкой длиной 45 мм
Обработанная механическим способом поверхность непористых материалов представляет
собой систему выступов и впадин, размеры которых могут отличаться друг от друга в
десятки и сотни раз. Например, средняя высота микронеровностей поверхности металлов,
определяемая как среднее арифметическое высот микронеровностей Н от гребня до дна впадины
(рис. 3), составляет для наиболее распространенных 3-6 классов чистоты обработки 63-6,3 мк;
длина макромолекул линейных полимеров составляет 0,1-10 мк, а поперечный их размер,
0,0003-0,0007 мк. При указанных соотношениях размеров макромолекул полимеров и
микронеровностей только часть поверхности входит в контакт с клеем, причем проникание
макромолекул во впадины ограничивается не только их размерами, но и силами внутреннего
сцепления в жидком клее, наличием адсорбированных на поверхности частиц воды и жира,
неоднородностью клея.
О том, что клей не заполняет всех микровпадин или заполняет их частично,
свидетельствуют результаты испытаний клеевых соединений металлов на действие воды и
растворов солей. Почти для всех клеев можно отметить проникновение агрессивных сред и
возникновение коррозионных явлений на поверхности металлов под клеевым слоем. При
недостаточной устойчивости металла клеевой слой может отделяться от поверхности в области
очагов коррозии. Это является результатом разрушения гребней растворами, проникшими по
наиболее крупным, не заполненным клеем впадинам.
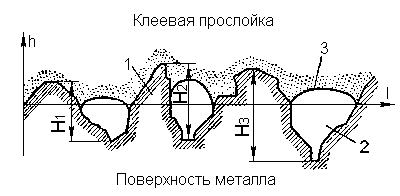
Рис. 3. Профиль сечения обработанной поверхности и граница клеевой прослойки.
1 - гребень; 2 - впадина; 3 - граница клеевой прослойки;
Для достижения большей химической стойкости соединения лучше склеивать поверхности с
высокой степенью чистоты обработки. Но, как уже отмечалось, такие соединения обладают
меньшей механической прочностью по сравнению с соединениями шероховатых поверхностей.
Прочность клеевых соединений возрастает пропорционально увеличению шероховатости.
Объяснение этому следует искать в физико-химических явлениях на границе клеевой прослойки,
главным образом в явлениях адгезии, поскольку когезионная прочность клея является величиной
постоянной для одного и того же технологического режима склеивания.
С увеличением шероховатости поверхности появляется больше активных центров, поэтому
адгезия возрастает. Когда шероховатость превосходит некоторый предел, рост прочности
соединений прекращается, так как происходит нарушение клеевой прослойки отдельными
крупными гребнями, которые противодействуют образованию упорядоченной структуры
макромолекул и созданию сплошной однородной клеевой прослойки.
При химической обработке поверхность металла имеет незначительную шероховатость,
тем не менее прочность соединений достаточно высока, что объясняется химической
активизацией поверхности, возможностью действия на ней различных сил адгезии. Разброс
показателей прочности при этом меньше.
Исследованиями установлено, что в зависимости от состава растворов, применяемых
для химической очистки поверхности, прочность склеивания и стойкость клеевых соединений
может быть значительно более высокой, чем только при механической зачистке или
обезжиривании органическими растворителями.
Существенно влияют на прочность соединений условия высушивания деталей после
химической обработки. Большинство металлов, главным образом легкие сплавы, покрываются
на воздухе заметными на глаз оксидными пленками, толщина которых быстро увеличивается в
начале высушивания. Поэтому склеивать надо немедленно после очистки поверхности. Следует
заметить, что при высушивании деталей в незагрязненной атмосфере влияние оксидных пленок на
прочность соединений незначительно. Наоборот, продолжительное пребывание обработанных
деталей в производственной атмосфере или на открытом воздухе значительно снижает прочность
сцепления клея с металлами.
На свойства клеевой прослойки, в частности на стойкость к коррозии и старению, на
водо- и теплостойкость влияет химическая активность металлов. При нагревании соединений
некоторые металлы (их окислы или компоненты сплава) влияют на клей каталитически, ускоряя
процессы деструкции полимера. От степени этого влияния зависит долговечность клеевых
соединений.
Прочность клеевых соединений зависит во многих случаях и от упруго-пластических
свойств металлов - предела текучести, модуля упругости.